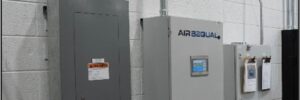
A lesser-known element of compressed air systems is that their design profoundly impacts the reliability and productivity of their operation. While the idea seems straightforward, there are many considerations that must be made early in the design phase; ideas that determine why an expert in compressed air system engineering is an invaluable part of your… Read more »